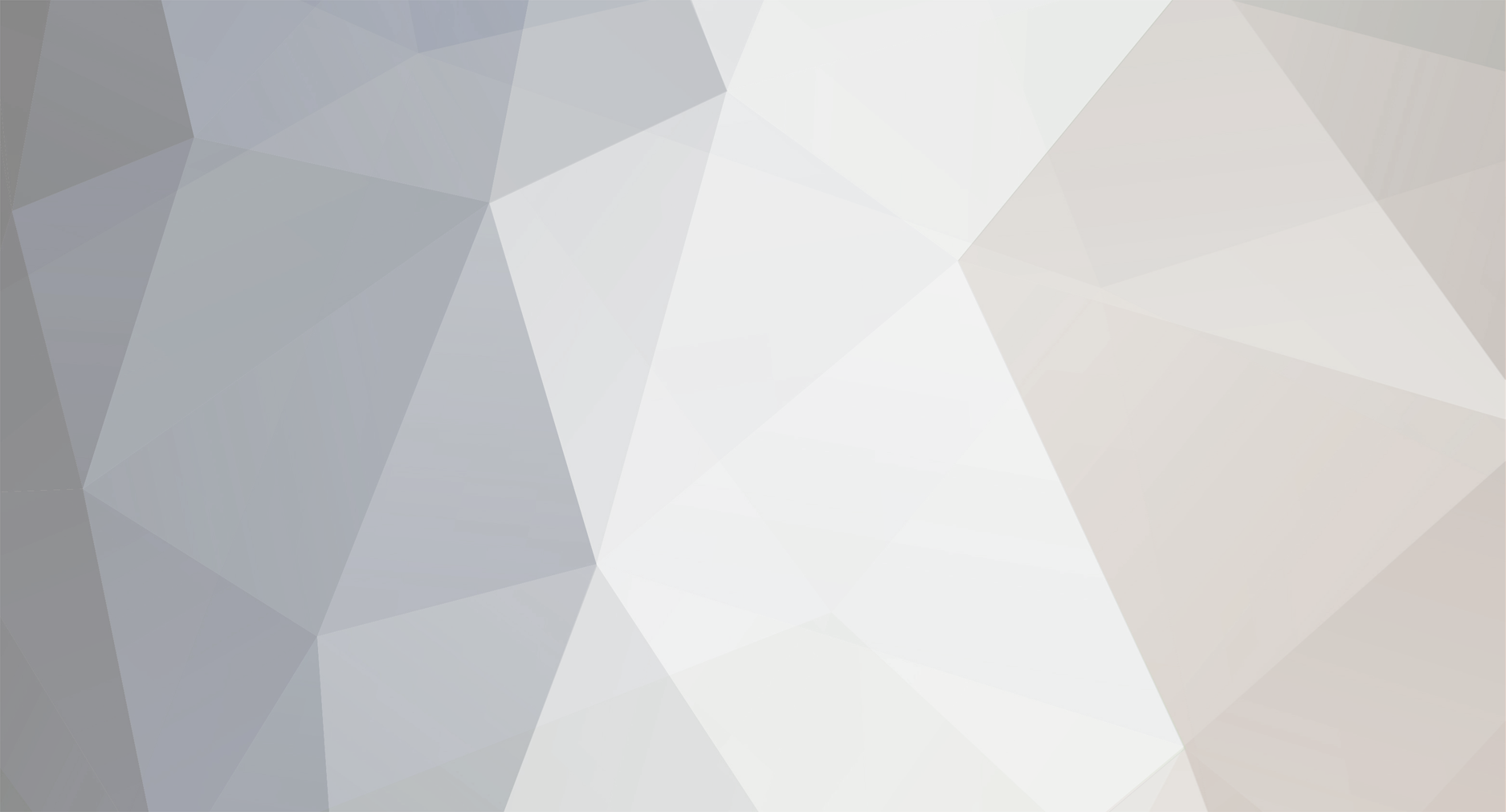
Neils TDi again
Members-
Posts
207 -
Joined
-
Last visited
Content Type
Profiles
Forums
Blogs
Everything posted by Neils TDi again
-
Why Has This Site Gone Quiet
Neils TDi again replied to baz69's topic in General Discussion and Nonsense
Like many forums and vehicle marks, they grow prosper and then grow old gracefully. A bit like me, I have sat watching for nearly two years maybe I should have been a bit more involved but like other forums and email chats sometimes it's not too friendly and the chill factor takes over. How about a few of the caption type fun responses to encourage a few more posts then it may wake us all up a bit. -
Rocking At Slow Speed
Neils TDi again replied to mrjay15's topic in Ford Galaxy Technical Section MK I MK II
I agree with Chrome its most likely to be dry CV joints mainly on the inner ones as they cause bad vibration at low speed or under harsh acceleration. -
I did mine too on a MKII but replace the clutch cylinder while your in there its a bugger to do any other time.
-
It would be worth checking with a digital multimeter the throttle pedal position sensor as it has two converging resistance tracks and if one is damaged or faulty then it get a missing signal when trying to relate pedal position to engine speed and this is normally only if you are giving it "beans" as the pedal is in a full down position which is not the normal driving area.
-
Vibration At 15mph
Neils TDi again replied to scotthaynes's topic in Ford Galaxy Technical Section MK I MK II
Scott if the vibration disappears as soon as you reduce power then it's almost certain to be the inboard drive shaft joint. The joint has a habit of wearing one of the three bearings and it then runs out of balance when under load. -
Injector Wiring Loom Or Glow Plug?
Neils TDi again replied to ronz's topic in Ford Galaxy Technical Section MK I MK II
I have to agree this is the most likely cause, just resolved the same issue doing my own pump and stat. -
01410 - Heater Over-temp
Neils TDi again replied to ronz's topic in Ford Galaxy Technical Section MK I MK II
One of the most common fault in the TDi is the water pump impellor becomes loose on the shaft and fails to pump the water around the cooling system. This results in over temperature and no heat in the interior heater. I just wrote a big post on replacing the water pump havinghad this very problem. -
Clutch Replacement On Mk2
Neils TDi again replied to Bigjeeze's topic in Ford Galaxy Technical Section MK I MK II
OK I have actually had to do this job it is not an easy one but it can be achieved. The most difficult part is that to remove the gearbox far enough to get the clutch cylinder out of the box it needs to be fully removed from the vehicle by rotating the gearbox after it is disconnected from the engine. The drive shafts must be diconnected and the subframe needs to be slackened to allow the gearbox to come out. The gear selector in the console needs to be locked in the correct position using a four mm pin. Then when the selectors are disconnected from the gearbox the ratchet locks can be set back to their original positions. The hydraulic pipes need to be disconnected from the cylinder before you remove the box. and it is the last part to be reconnected. Make sure you have a good size hyperdemic syringe to make the refilling of the master cylinder easier. Although I did this it did take about 12 hours from start to finsh and I didnt replace the flywheel. I did replace the entire clutch and slave cylinder/release bearing and it did get rid of the noise and the feeling of hesitance when lifting the pedal. -
Having had the temperature fault of high temp on high loads and normal on running round the town i decided it was time to bite the bullet and change the water pump. First order new pump, alternator belt, thermostat and cam belt. ( i would never change the water pump without changing both belts but in particular the Cam belt as it is the driver of the pump. Second make sure you have the right pump and belts ( europarts managed to get at least the pump wrong). This process is my own and it may or may not be acceptable to others but I did it and it may help others. First jack up the car and remove the undershield. and the offside wheel. Remove the Plastic cover and foam sound deadening material from the top of the engine. Remove the Air filter box complete with MAF by disconnecting the main air pipe from the box and removeing the allen capscrew that secures the air box to the body. Using a suitable protection material (i used a wooden blockwrapped in lots of cloth) and a jack support the engine from underneath (protection cos i jacked against the sump, not recommended but what i did). Undo the three 16mm bolts that secure the offside engine mount to the engine. Undo the two 16mm nuts that secure the mounting bracket to the engine mount on the body. Using a torx driver remove the engine mounting from the body. Using a ring spanner loosen the two 16mm bolts that hold the top of the engine mounting to the engine, then undo the three 13mm bolt that fit it to the engine mounting post. Using a 17mm open ended spanner release the tension on the alternator belt and remove the belt from the alternator pulley. A five mm drill can be used to lock the tensioner in the released position if you need this when fitting it back together. It passes through the lug and through the main tensioner bracket. Using a 13mm socket remove the alternator belt tensioner assembly. Lower the engine sufficient to be able to see the crack shaft pulley from the wheel arch area, remove the 13mm bolt that secures the power steering pipe to the engine mounting. Slacken the last 16mm bolt that secures the engine mounting plate to the bottom of the engine. Remove the plastic cover disc from the main crankshaft pulley. Remove the four capscrews that secure the pulley to the crank, and remove the pulley. The pulley has five holes as there is a location spigot on the face of the bottom cam belt pulley. Remove the four 10mm screws which secure the bottom cam belt cover and remove the cover. Lift the engine back and remove the two 16mm bolts that secure the engine mounting plate and then remove the central mounting post which will be loose when the 16mm bolt is removed. Remove the engine mounting plate. Unclip the top cam belt cover a clip is on the front and rear of the cover. remove the remain central belt cover from the engine. Before removing the cam belt the postion of both the crank shaft and the cam shaft should be locked. Ideally use a locking kit for the crank and cam or alternatively note the position of the lower pulley and cam pulley so that when refitting and tensioning the belt the pulleys must remain in the correct position. I marked the lower pulley with a mark of white paint, and set the cam belt pulley to align one of the lugs on the back plate of the cam shaft pulley with the edge of the rocker cover. Slacken the adjuster and remove the timing belt. Remove the three 10mm bolts from the water pump housing all that are within the area covered by the cam belt cover. Gently prise the water pump out as there is an Oring on the pump to seal the water system. remove the pump. Reftting is the reverse of the removal but great care must be taken to align the pulleys on the cam belt when refitting the new belt and ensure you use a torque wrench when refitting all the parts. If you have had this temperature problem you may want to replace the thermostat at the same time and i would do this as a matter of course. To do this remove the two bolts that secure the alternator in place, then remove the two 10mm screws that retain the thermostat housing which is behind the alternator and connects the main radiator hose to the engine, it has the thermostat inside the palstic hosuing. Replace the oring at the same time if you change the thermostat. To aid fitting the cam belt I removed the additonal idler wheel until the belt was fitted on the main pulleys and allowed the water pump to be loose only tightening the pump and idler when the belt was on. I would like to add the photos of the job but I did it by the light of an LED wander lamp as I was forced to do it at night in the rain.... Once a level of confidence has been achived this can be done in under two hours, I ended up doing it twice as I said I intially had the wrong pump but it wasnt evident until I had removed the pump on the first attempt. First time i did this it took about four hours on the second night knowing where all the bolts were and the sequence of removal I did it in about 1 hour 40 minutes. Hope this gives some other a bit more confidence to have a go.
-
The bottom engine mount that you are describing is the anti roll mounting in the middle of the engine at the rear. Repeated failure of this bolt would indicate a potential set of circumstances: 1) The clutch release bearing is sticking and allowing the application of torque to be applied as a rapid introduction of force (the take off or gear change would feel jerky or snatchy) 2) The roll restrictor its self may have degraded, the rubber may have deteriorated to the point it is not absorbing the shock of the application of torque. 3) The dual mass flywheel is worn out causing the rapid application of force. Ultimately the driving force of the engine has to push against a part of the body to push the wheels round, equall and opposite forces, the roll restrictor prevents the engine winding itself outof the body and forces the wheels round. So a new part and a new bolt may stop this repeating, just replacing the bolt is just fixing the symptom and not repairing the cause. Best of luck
-
As per normal about as much interest in meeting anything other than at a petrol pump in service station. Why is this called a club it has less club than a golfer on holiday. Is anyone going to go to Billing and represent this forum or is it another complete waste of time by your favourite MOD. ??????
-
1.9 Tdi Advice Needed
Neils TDi again replied to me myself and I's topic in Ford Galaxy Technical Section MK I MK II
The fuel lift pump diaghram is the nromal cause of this and its pretty easy to change. I had a 1.9 TDi with 300k miles on the clock and it was still going (albiet an injector was blowing) then some twat wrote it off for my sister. -
A Quick Question..
Neils TDi again replied to mumof4's topic in Ford Galaxy Technical Section MK I MK II
MAz Before you go spending large amounts on dosh on a rack and pump try putting a new power steering belt on the Gal from my own MK1 as you remember it also had the same problem and that was down to the belt being worn rather than loose, it allowed the belt face to slip in the pulley and then when the demand for pressure in the pump was increased everything juddered. Good luck with the oil but I would still be looking for a change rather than just the top up as when it gets that low its likely to have over heated the existing oil. -
I would first check your drive shafts as they tend to "go off centre" with the torque when they begin to wear severely.
-
Goodbye And Thank You
Neils TDi again replied to PhilT's topic in Ford Galaxy Technical Section MK I MK II
Come follow my link its a good forum for the BMW. -
I aint saying nowt either !!! Anyways if its too big the effect aint anything like it should be........ and as for the zip not being appropriately sized you can get them to fit a frame tent so it shouldnt be a problem getting one for M.
-
Is that M of 4 in that picture or do my eyes deceive me ? Running.......................
-
Grumblin... Comin Back..
Neils TDi again replied to mumble_bee's topic in General Discussion and Nonsense
SAD -
Acouple Of Things!
Neils TDi again replied to romseygalaxy's topic in Ford Galaxy Technical Section MK I MK II
The resistor pack acts as a voltage splitter for the different speeds and is normally located in the air plenum so the flow of air in the fan cool sthe resister and stops it melting, if it fails it melts as the fan begins to run ever slower. Vicous circle the fan is controlled by the resistor and the fan circulates air to cool the resistor if it begins to fail and the resistance goes up then the fan slows and the cooling is reduced so the resistor fails even more. and on we go. Not at home at present so cant even access the TIS to get pictures maybe a friendly MOD will do something for you. -
Acouple Of Things!
Neils TDi again replied to romseygalaxy's topic in Ford Galaxy Technical Section MK I MK II
Nothing happening when selecting Air Con normally indicates that the pressure switch is not recording a differential pressure therefor its possible you need to "re-gas" but this normally caused by a leak so it needs to be checked. FUse 30 blown, mainly due to a faulty resister pack in the blower box. if you select high speed on your fan it will probably blow again. Both need repair / replacing. -
Start both when the 4 runs out turn the 4 over elapsed time = 4 mins when the 7 runs out turn both over again elapsed time = 7mins (the 4 has run for 3 mins.) when the 4 runs out turn them both over again elapsed time =8 mins when the seven runs out elapsed time=9 mins there you go. done. :lol:
-
3) He is playing Monopoly.
-
Wobble Whilst Accelerating
Neils TDi again replied to Coxsey's topic in Ford Galaxy Technical Section MK I MK II
COxsey if you are replacing the shaft (eg with the original) then it is accepted that you should wherever possible align the shaft to the same position however fitting a new one this becomes impossible. However if you have replaced just oneof hte joints you MUST make sure the orientation of hte joint is correct as to the original or cyclic forces will cause an out of balance rotation and vibration will result. -
Gearbox Stuck In First
Neils TDi again replied to PhilT's topic in Ford Galaxy Technical Section MK I MK II
on the top of the gearbox the selector shaft should be held in with five 10mm af bolts (or Cap screws cant remember which) this will enable the selector assembly to be lifted out. You cannot remove the main battery support bracket but removing the bolts enables you to drop the gearbox enough to remove the selector shaft. Supported on a jack I hasen to say. -
Gearbox Stuck In First
Neils TDi again replied to PhilT's topic in Ford Galaxy Technical Section MK I MK II
MK1 TDi gearboxes have a habit of breaking the 7mm bolt that holds the selector onto the shaft, can be replaced from above by removing the battery tray but leaves the head of the broken bolt in the gearbox, hopefully in an area where it wont cause a problem. I have had two go like this and although it is a cheap fix (the bolt came out of a Peugeot 405 deisel pump) its also likely that most would recommend a gearbox strip to solve the problems.